Team Cardata
5 mins
What is the Process for Updating Blind Spot Detection in Company Vehicles?
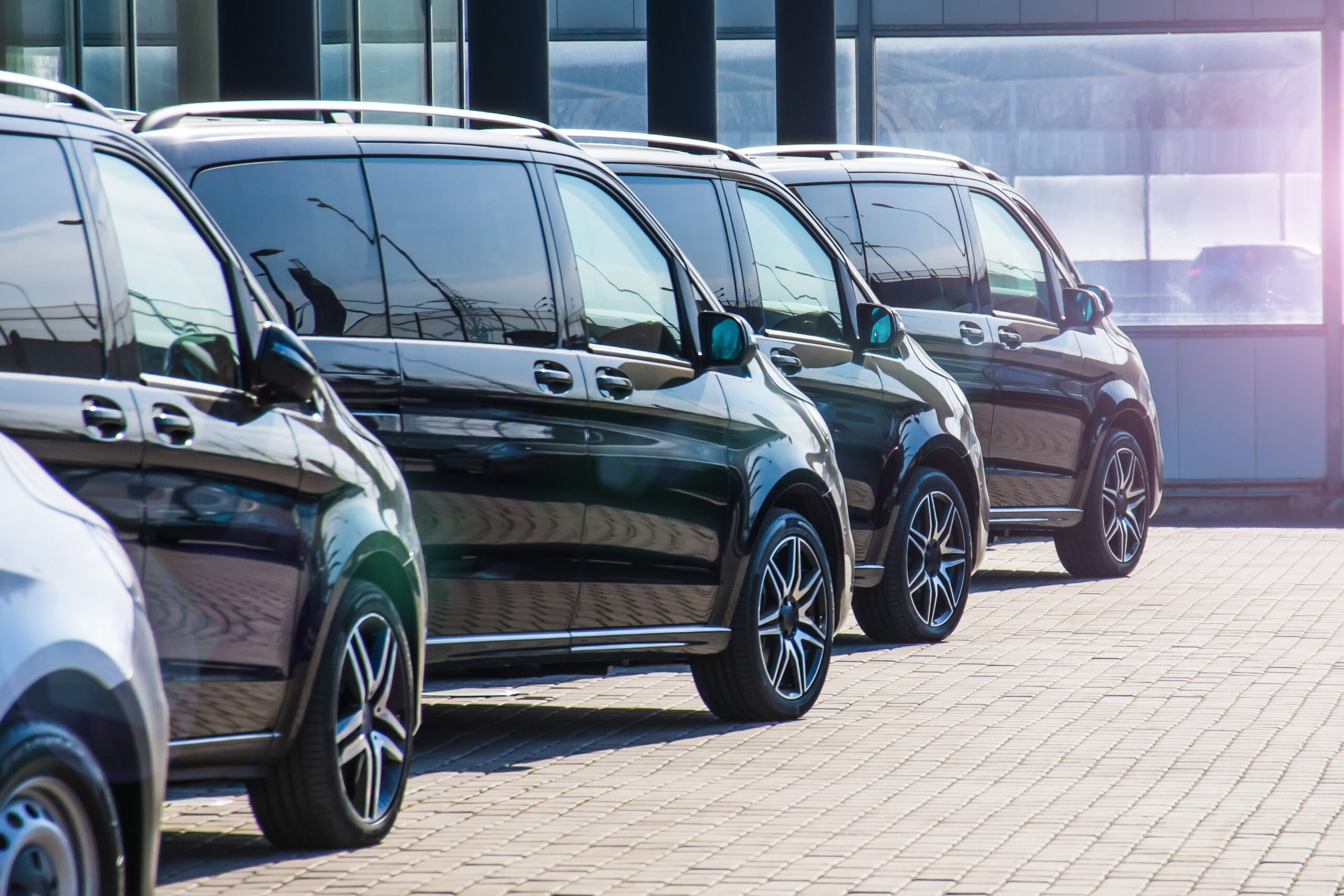
Speak to an Expert
Book a CallBlind spot detection (BSD) systems are no longer optional in commercial fleets. As part of advanced driver assistance systems (ADAS), they play a pivotal role in reducing vehicle collisions during lane changes, merges, and high-speed transitions. Updating these systems—through software, hardware, or training—is a structured, compliance-driven process that engages multiple stakeholders from fleet technicians to safety compliance officers.
Why BSD Updates Are a Safety Imperative
Motor vehicle crashes are the leading cause of work-related fatalities in the U.S., and many occur during working hours, often involving commercial fleets. Blind spot detection mitigates this risk by alerting drivers to vehicles they may not see in adjacent lanes. This is particularly critical for fleets operating in urban environments or with large vehicles that have limited mirror visibility.
BSD and blind spot warning (BSW) systems reduce accidents and enhance driver awareness. They work by monitoring adjacent lanes using radar or camera sensors and issuing visual, audio, or tactile warnings when another vehicle enters the monitored zone.
Methods for Updating Blind Spot Detection Systems
BSD updates take two primary forms: over-the-air (OTA) software updates and physical hardware retrofits. OTA updates are often issued by OEMs and can include improved sensor calibration, detection logic refinement, or integration with new telematics data.
In contrast, retrofitting older vehicles involves the installation of aftermarket sensors and visual alert systems. These require careful placement and calibration by trained fleet technicians. Incorrect installation or calibration may result in false positives or detection blind spots, undermining the system’s safety value.
Fleet Technicians: Key Players in System Updates
Fleet technicians are responsible for diagnosing, updating, and maintaining BSD systems. Their roles encompass brake repair, electronic diagnostics, and ADAS system checks. Technicians must also adhere to safety regulations and understand the vehicle’s electrical architecture.
Routine updates often include performing confirmation tests, where another vehicle enters the blind spot to test sensor response. This mirrors standardized testing procedures developed by the National Highway Traffic Safety Administration (NHTSA).
Insurance, Licensing, and Regulatory Compliance
Updating BSD systems affects more than just mechanical or digital systems. Once updated, company vehicles may require revised business use endorsements or commercial vehicle classifications. Commercial vehicle insurance can cost twice as much as personal coverage, especially for vehicles used in high-mileage or delivery-intensive industries.
Inadequate insurance adjustments or misreported usage types can leave companies vulnerable to denied claims. BSD installation must be logged and included in vehicle documentation for regulatory and insurance compliance. Cardata’s insurance compliance protocols, including its 12-point audit per driver, help mitigate these risks.
Integration With Fleet Telematics
Fleet telematics platforms enable real-time oversight of BSD functionality, update schedules, and diagnostic alerts. Connected systems such as Cardata Cloud centralize vehicle data, flagging units overdue for calibration or software updates. This allows proactive maintenance, reducing the chances of system failure or liability exposure.
These tools also assist in managing driver records, licensing status, and update compliance. They create a fully auditable system that supports tax compliance and minimizes administrative overhead.
Maintenance and Testing Protocols
Preventive maintenance protocols should include periodic inspection of radar sensors, wiring integrity, and software diagnostics. BSD sensors are typically located on or near bumpers, making them vulnerable to impact damage or debris interference. Testing protocols should mirror real-world use cases and include the NHTSA’s blind spot confirmation methods.
Fleet technicians and safety officers must document all test results and maintenance records to meet OSHA and DOT requirements.
Driver Training and Usage Education
Installing or updating BSD systems is only effective when drivers understand how to use them. Training should emphasize that these systems are supplementary and not a substitute for visual checks. Defensive driving courses that incorporate BSD usage training have been shown to reduce accident rates and improve driver accountability.
Companies can include BSD module training during onboarding or annual safety reviews. Incorporating feedback loops—such as driver-reported alerts or malfunction reports—ensures ongoing system reliability and user engagement.
Documenting the Update Process
Every BSD update must be documented thoroughly. For fleets using Vehicle Reimbursement Programs (VRPs) such as FAVR, updates to safety features like BSD may influence vehicle eligibility, reimbursement rates, or tax treatment. Updated documentation should include:
- Vehicle ID and license plate
- Date and nature of update
- Software version or hardware part numbers
- Installer name or technician ID
- Post-installation test results
- Updated insurance policy endorsements
Maintaining this data supports tax-exempt reimbursement programs, reduces audit risk, and enhances overall fleet governance.
Promoting Safety Culture Through BSD
Blind spot detection systems are more than a technical upgrade—they are a statement of intent. Companies that prioritize BSD updates demonstrate a commitment to driver safety, risk reduction, and regulatory compliance. This improves workplace morale and may even reduce turnover by enhancing employee confidence in their equipment.
Involving drivers in BSD policy creation and reporting processes further strengthens a culture of shared responsibility.
Conclusion
Updating blind spot detection systems in company vehicles is a multi-step process that involves more than just installing new sensors or pushing software patches. It intersects with safety protocols, insurance policies, driver training, and compliance obligations. As federal regulations move toward incorporating BSD systems into New Car Assessment Programs (NCAP) starting in 2026, the urgency for businesses to implement structured BSD update procedures will only grow.
Through robust documentation, telematics integration, driver engagement, and professional fleet management, companies can transform BSD systems into a cornerstone of safety and compliance.
Disclaimer:
The content provided in this blog is for informational purposes only and is not intended as legal, financial, or tax advice. While every effort has been made to ensure the accuracy and reliability of the information at the time of writing, Cardata and the author assume no responsibility for any errors or omissions. Readers should consult with a qualified professional to determine how any information discussed may apply to their specific circumstances. Any opinions expressed are those of the author and do not necessarily reflect the views of Cardata.
Share on: